Three-dimensional printing has been applied to handguns, rockets, hypersonic jet engines, bicycles, ears, objects d'art, and now submarine-launched ballistic missiles (SLBM). Lockheed Martin has announced that the first 3D printed components for an SLBM flew this week on test launches of three unarmed US Navy Trident II D5 Fleet Ballistic Missiles from a submerged submarine in the Atlantic Ocean. The component tests, which were conducted from March 14 to 16, are part of Lockheed's program to create an all-digital manufacturing process.
The component in question was a "connector backshell," which fits over cable connectors and protects them from damage or accidental disconnection. It was designed and manufactured using entirely digital processes with 3D design files used to guide a 3D printing machine.
The additive printing process used to create the inch-wide (2.5 cm) connector backshell involves a fine layer of aluminum alloy powder being laid down and a laser or electron beam, guided by a computer, fusing the powder into a solid metal pattern corresponding to a layer in the finished product. The machine then lays down another layer of powder and the process repeats itself until the component is complete. All that is then needed is for the excess dust to be brushed away and the component smoothed and polished. The process reduces waste material and, according to Lockheed, takes only half the time of conventional methods.
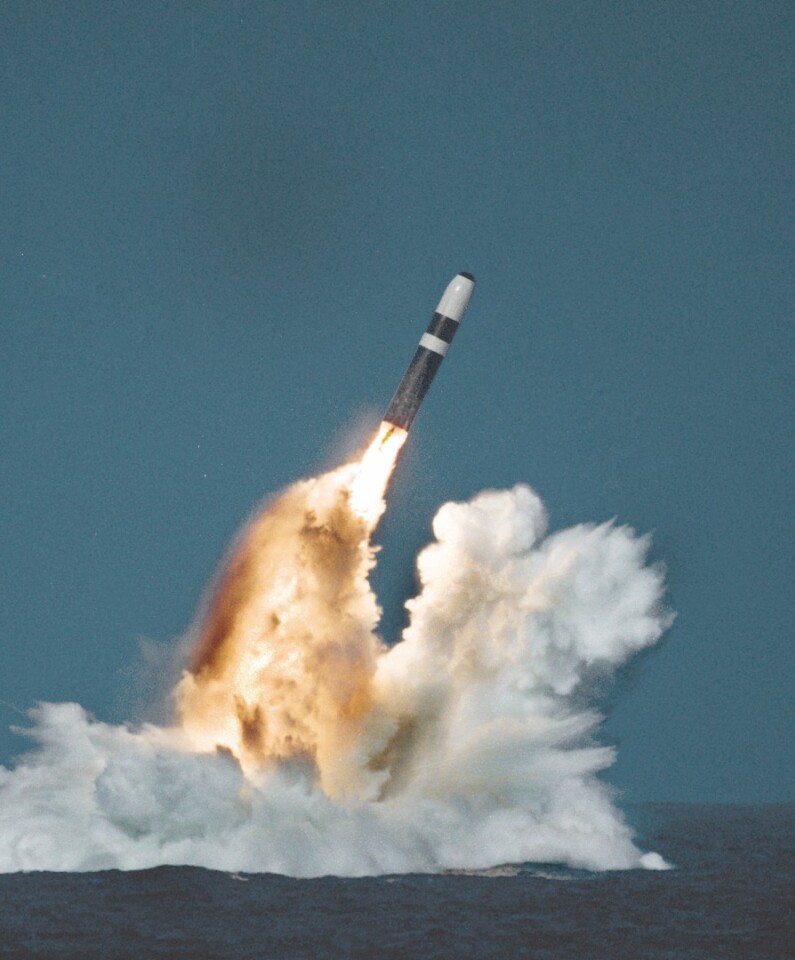
The three flights were carried out under the Follow-on Commander's Evaluation Test of the Trident Strategic Weapon System and were the latest of 160 test flights of the D5 missiles carried out since the design was completed in 1989. As in other tests, the D5 missiles were converted for testing with kits that include safety devices and flight telemetry systems.
The Trident II D5 is currently in service with on the US Navy's Ohio class and the Royal Navy's Vanguard class strategic nuclear ballistic missile submarines. Replacing the earlier Polaris and Poseidon missiles, the sixth-generation, three-stage Trident has a range of over 4,000 nm (4,600 mi, 7.400 km) and carries Multiple Independently Targeted Reentry Vehicles (MIRV).
Source: Lockheed Martin