Australia’s motorsport mecca is in the midst of its first major facelift in 14 years, with the island’s hallowed 4.4 km (2.7 mile) race circuit being treated this week to a $3 million resurface to create the smoothest, fastest race track in the world. The Phillip Island circuit, which already produces the fastest average speed lap in both MotoGP and WSBK motorcycle racing, is set to get even faster in 2013 with the new track surface.
The resurfacing of the entire track (and some extra areas) involved the unusual measure of erecting an asphalt batching plant onsite to deliver the 5,000 tonnes of the specific asphalt mix required, a huge undertaking that is not normally done for jobs under 25,000 tonnes. This enabled the asphalt to be laid at the higher temperature of ~160ºF and to incorporate a polymer modified binder which would not have been possible had the material been delivered from off site. The plant was shipped to the island last month in nine over-sized low loader trailers and covers the entire TV compound and support paddock.
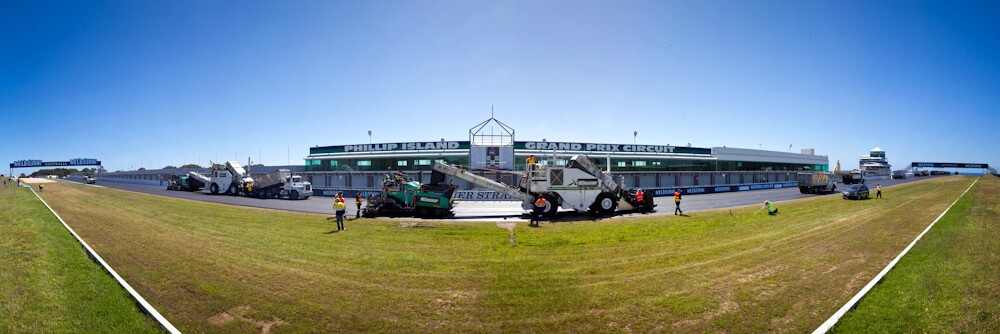
The higher temperature and polymer binder were necessary to ensure the laid asphalt had the desired density, grip and robustness to meet the demands of not only premier class motorcycle racing but also heavy V8 saloon cars and other high-stress 4-wheeled traffic. In June, engineers used a three dimensional laser survey to profile the track to within 3 mm and last week up 40 mm was milled off the old surface to prepare a perfectly smooth bed for the new asphalt. This week over 35 heavy machines and 70 contractors were involved in a massive logistical operation that saw five meters of track laid every minute.
The asphalt mix was developed by the circuit managing director, Fergus Cameron in conjunction with construction group Downer Australia, to achieve the aim of a hard, durable and smooth surface resistant to the pressures of racing.
“The asphalt mix will remain our secret Phillip Island recipe,” said Cameron. “All I’ll say, is it is designed to make the cars and bikes go faster. On a scale of 0-110 on a friction coefficient test the old surface was at 54 or 55 and the new surface is at 78, so the new surface is much grippier.”
The circuit which is used 300 days a year for racing, testing and ride and drive days should have a ten year life span and is designed to satisfy the needs of riders and drivers.
When asked whether there needed to be any compromises made to be able to cater for both cars and bikes, Cameron had this to say: “There’s not a lot of difference in what they require but there is a lot of difference in the way they affect the track. The old C323 binder that we used before was very malleable and it was surprising just how much elasticity it still had in it. We have run V8 Supercar races here for the last three years and I’m sure it had an effect on the roughness of the track surface. That’s what the polymer modified binder will give us – a much harder surface and we believe the chance of the surface becoming bumpy is now much less. The track has to be resistant to the pressures of cars, yet maintain the smooth surface that’s imperative for the fastest bike racing in the world,” While the likes of world superbike’s Max Biaggi and MotoGP’s Casey Stoner hitting speeds of over 320 kph (199 mph) heading down the island’s iconic Gardner Straight, the V8 Supercars also give the place a serious knock. While the cars clock a top straight speed of only (!) 280 kph (174 mph), they are faster than the bikes through the corners, applying added stresses to the track. The exact recipe may remain a secret to us but Cameron has already supplied a detailed analysis of the new surface to the racing tire manufacturers who will then use this information when developing new tires to suit the track (an entire science in itself which we investigated with our story on Pirelli’s development efforts for WSBK).
The resurfacing is a logistical undertaking of impressive proportions, with the raw materials being deposited into huge hoppers in the batching plant, and then transferred along conveyor belts into the plant’s “mixing bowl.” The asphalt comes out at 172 degrees, and is taken by truck the 100 meters or so to the track where it is transferred to a shuttle buggy. From the shuttle buggies, the asphalt is deposited into two giant pavers which lay the material, followed by a steel roller and a rubber paved roller that compress the surface to a perfect finish. The two pavers work in echelon, only 20 meters apart, to ensure there is no middle join in the circuit. They pave on average five meters a minute starting on Gardner Straight, through each iconic corner including the high speed Doohan Corner, the recently named Stoner Corner, out to Siberia, up through Hay Sheds and over Lukey Heights. The 18 month development period for the design and engineering of the resurfacing also included a trip by both Cameron and the contractors to consult with the Mugello circuit in Italy, which is currently regarded as having the flagship racing surface in the world.
“The field is littered with examples of where racetracks have got it wrong in terms of the mix that they’ve put down, particularly with street circuits where they’ve unraveled. There’s been some exhaustive testing done in relation to different mixes and different designs and we’re pretty comfortable we’ve got it right.”
The circuit will be ready for racing for January’s Island Classic for historic bikes and then in February will host the world superbike riders for final pre-season testing and the 2013 opening round on February 24.