Inspired by origami and children's pop-up books, Harvard engineers have pioneered a means of mass-producing bee-sized flying microrobots. The breakthrough mechanizes the already state-of-the art process of making Harvard's Mobee robots by hand, by mass producing flat assemblies by the sheet which can be folded and assembled in a single movement. The technique, which cunningly exploits existing machinery for making printed circuit boards, can theoretically be applied to a multitude of electromechanical machines.
The art of flat
Prototypes of the mass-produced Mobee (short for Monolithic Bee) consist of 18 laminated layers of carbon fiber, polymers and ceramics, laser cut into an intricate form that incorporates 22 folding joints, and housed in a dedicated assembly scaffold (which itself has an additional 115 folding joints).
It's these folding joints - hinges, basically - that allow the robot to be assembled in a single movement. The scaffold is crucial to this process, providing two horizontal plates which can be pulled apart, erecting the Mobee in the process.
The new process allows for scores of robots to be manufactured at once on a single sheet.
Machines making machines: automating the artisanal
The switch from hand-made robots to automated manufacture has all but eliminated failures. Only months ago, the Harvard team was folding and gluing parts by hand using techniques they had developed in-house. "You'd take a very fine tungsten wire and dip it in a little bit of superglue," said Pratheev Sreetharan, co-developer of the technique with J. Peter Whitney. "Then, with that tiny ball of glue, you'd go in under a microscope like an arthroscopic surgeon and try to stick it in the right place."
State-of-the-art this process may have been, but only 15 out of every 100 robots manufactured actually worked. Automation not only eliminates human error, but increases the options basket in terms of both materials and manufacturing processes. "The ability to incorporate any type and number of material layers, along with integrated electronics, means that we can generate full systems in any three-dimensional shape," said principal investigator Rob Wood. "We've also demonstrated that we can create self-assembling devices by including pre-stressed materials."
The manufacturing is so accurate, in fact, that the team is at pains to measure it, though Sreetharan says it is "better than 5 microns everywhere".
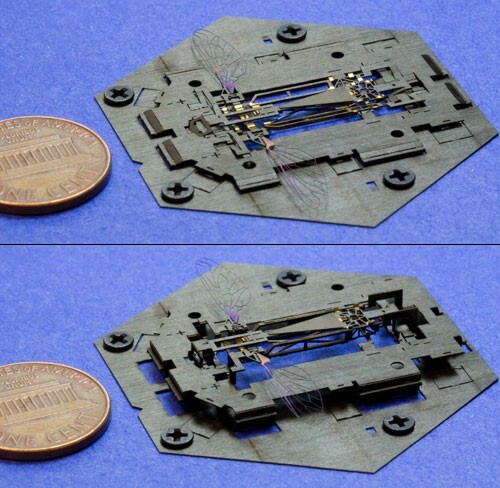
Diffusion: automating the making of small, complex machines
Because the process is so adept at embedding electronics into machinery, it is particularly suited to the manufacture of small electromechanical machines, or those with tightly integrated electronics. Keeping the weight of the Mobees down is so important, the design team cannot afford to introduce structural elements that cannot also contribute to the robot's electronic functioning. The entire product, scaffold included, is only the size of a US quarter and weighs only 90 mg, or a mere three thousandths of an ounce.
That the process builds upon the techniques used to created printed circuit boards is potentially of great significance. Harvard claims that the tools needed to adopt the technique are already widely used, which means the technique might see rapid diffusion - should the demand for products prove widespread. Harvard has filed numerous patent applications associated with the process, and is working with business to "identify disruptive applications in a range of industries."
An excellent video (and I do not use the term lightly) showing animations and video footage of the assembly of the Mobee is below.
Source: Harvard