Back in 2011, we wrote about a fascinating new way to heat-treat regular, cheap steel to endow it with an almost miraculous blend of characteristics. Radically cheaper, quicker and less energy-intensive to produce, Flash Bainite is stronger than titanium by weight, and ductile enough to be pressed into shape while cold without thinning or cracking. It's now being tested by three of the world's five largest car manufacturers, who are finding they can produce thinner structural car components that are between 30-50 percent lighter and cheaper than the steel they've been using, while maintaining the same performance is crash tests. Those are revolutionary numbers in the auto space.
Darren Quick did a good job explaining exactly how Flash Bainite is produced in our original story, but in basic terms, you take regular, off-the-shelf AISI1020 carbon steel, and instead of heat treating it for 10 minutes like costly alloyed steel, you put it through a roller-driven system that induction-heats and liquid-cools the steel in a matter of 10 seconds or so.
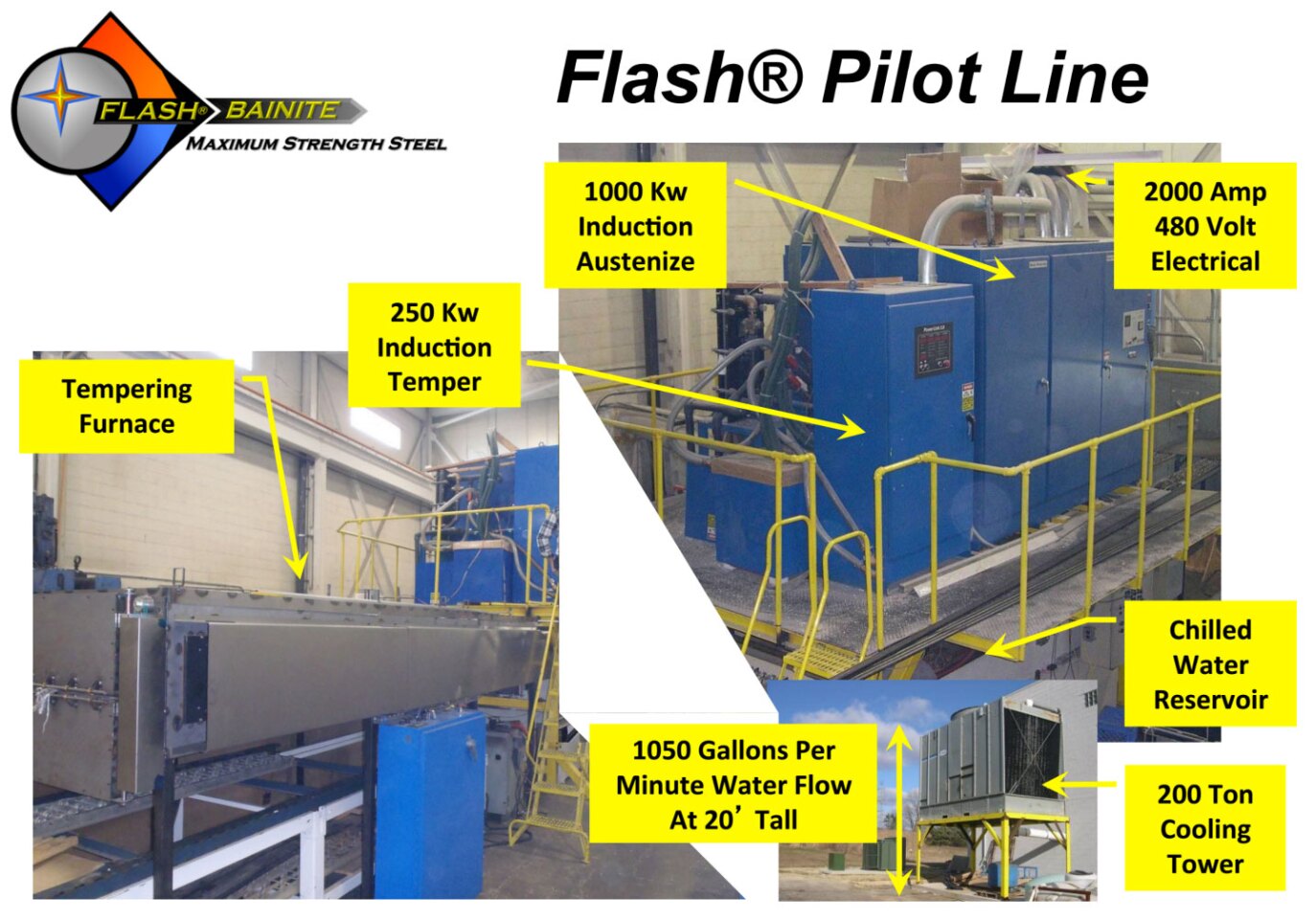
Generally, when you choose steel you're trading off between strength and ductility. The hardest steels are the martensitic types, but their crystalline structure makes them brittle and prone to cracking when you press or bend them, so they need to be hot pressed. Flash Bainite breaks this rule by delivering a specific strength some 7 percent higher than martensitic steel but staying remarkably bendable to the point where it can be cold pressed into shapes. The quick heating and cooling stages produce a unique mix of fine martensite, bainite and carbides – if you want to get all metallurgical about it, knock yourself out.
With such characteristics, you could theoretically take anything you're making out of martensitic steel and make it stronger and vastly cheaper, or take many shapes you're cold pressing out of more ductile steel and use vastly thinner Flash Bainite to get the same strength. It sounded almost too good to be true, but recent testing from a number of different parties appears to be validating the original findings.
In July 2011, US Army tests called it "an extremely energy efficient and environmentally friendly process" and concluded that "the costs to produce Flash Bainite should be extremely reasonable and could enable widespread use for applications requiring very high strength and adequate elongation, ductility, and toughness. Current opportunities for flash bainite include armor and vehicle applications requiring ultra-high strength steels for high specific strength, weight reduction, and high cycle fatigue enhancement."
In 2013, a few auto manufacturers (who can't be named due to NDAs) began running a series of tests to see how Flash Bainite might perform in an automotive setting. Could it be cold pressed into the kinds of challenging shapes required by automakers? In short, yes. Flash 1600 (Flash-processed AISI1020) forms as well as the leading cold-stampable "advanced high strength steel" DP1180 that's only 75 percent the strength. Here are some sample parts displayed in March 2015, cold pressed with no noticeable thinning:
These parts were created in the same sizes and thicknesses as the OEM parts, so there's no weight saving per se, but the simple and energy-efficient nature of the Flash forming process makes them 1/3 to 1/2 less expensive than the process currently used in manufacture.
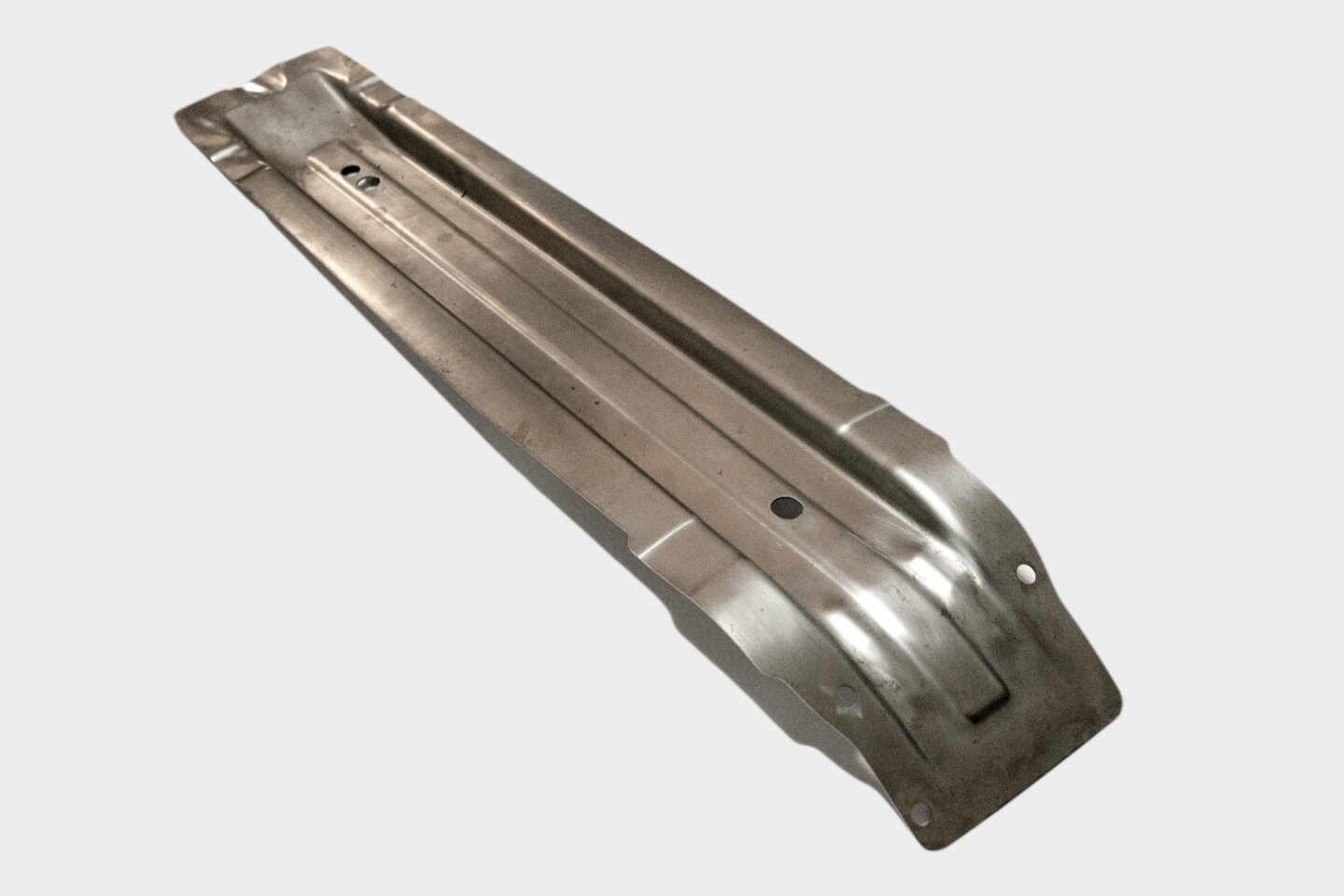
As this data became available, other auto manufacturers have started dipping toes in the water as well. The Flash Project's Gary Cola tells us of another major manufacturer that used Flash processed tubing to create car door impact beams, roof rails and other parts that were built into full cars, then roof crush tested to high test results.
"This OEM found that Flash 1500 could offer a 1/3 mass reduction and cost savings over the 'industry standard' DP1000 known at the time to be the strongest hydroformable tube," Cola says. "During this development, it was discovered that Flash 1500 (Flash-processed AISI1020) could be formed into very tight bends, almost as tight as simply folding a sheet of paper."
In Flash 1500 energy absorbing crush in this story's lead image, the bends are twice the strength of the DP780 cans in cars today.
Another major manufacturer "that makes 10 million vehicles per year," according to Cola, tested Flash-processed steel on a structural/safety component of a car that is 3 mm thick and 3 lb (1.4 kg) in weight in its current form. Using the flash treatment, a part was created that weighs 2 lb (0.9 kg) at 2 mm thick, and passes all the same tests – and the OEM estimated it could be made at a cost savings.
There are only three OEMs that can claim that kind of manufacturing capacity in the world. Only one of them is headquartered in Detroit where the Flash Bainite team is based, and it conveniently happens to be locked in a war of words with a competitor that has chosen to go to aluminum truck bodies instead of steel. Cola notes, "while aluminum is good for hoods, decklids and door skins, Flash offers higher strength per pound for structural safety components."
In short, Flash Bainite is starting to look suspiciously like the real deal, pointing the way towards significantly lighter cars that are less expensive and more environmentally friendly to produce, and every bit as safe in a crash – and of course, that's just in the automotive world.
Another factor in Flash's favour is an extremely low capital cost of entry for companies looking to get involved in the manufacturing process.
"The entry point for Flash equipment is about US$300K and a one car garage, while large format equipment would only cost $5M to generate about $75M in annual sales," Cola tells us. "Imagine if 100s of fabrication shops around the country could make higher performing steel than the Big Steel Industry can in their $400M seven-story tall furnaces."
Having said that, there's currently no large scale manufacture up and running. Cola and the Flash Project team are working toward developing their own commercial manufacturing operation, but hoping to license the Flash technology to other entrepreneurs to get it out into the market. If the business side is managed well, this looks like a genuinely disruptive shift in manufacturing. We'll keep an eye on it!
Source: Flash Bainite