Telescopes are very simple devices in theory, but getting one to work in space means a complex assembly of mechanical parts that is expensive, difficult to build, and hard to operate in the hostile environment outside the Earth’s atmosphere. To simplify things, NASA aerospace engineer Jason Budinoff is working on the first space telescope made entirely from 3D-printed parts.
The telescope is being fabricated using an additive printing process where the structure is built up layer-by-layer, by fusing a metal powder using a computer-controlled laser beam working from a 3D digital file. As each layer is created, more powder is laid down and the process is repeated. When finished, the excess powder is removed and the component is polished.
This process allows for very fast prototyping, reduces fabrication costs, and because it can create very complex structures, the number of components needed to make a space telescope are drastically reduced. Some structures, such as the telescope's optical baffles, can be made in one piece, which wouldn't be possible using conventional techniques. NASA says that using the technique, the first 3D-printed telescope will only take three months to complete.
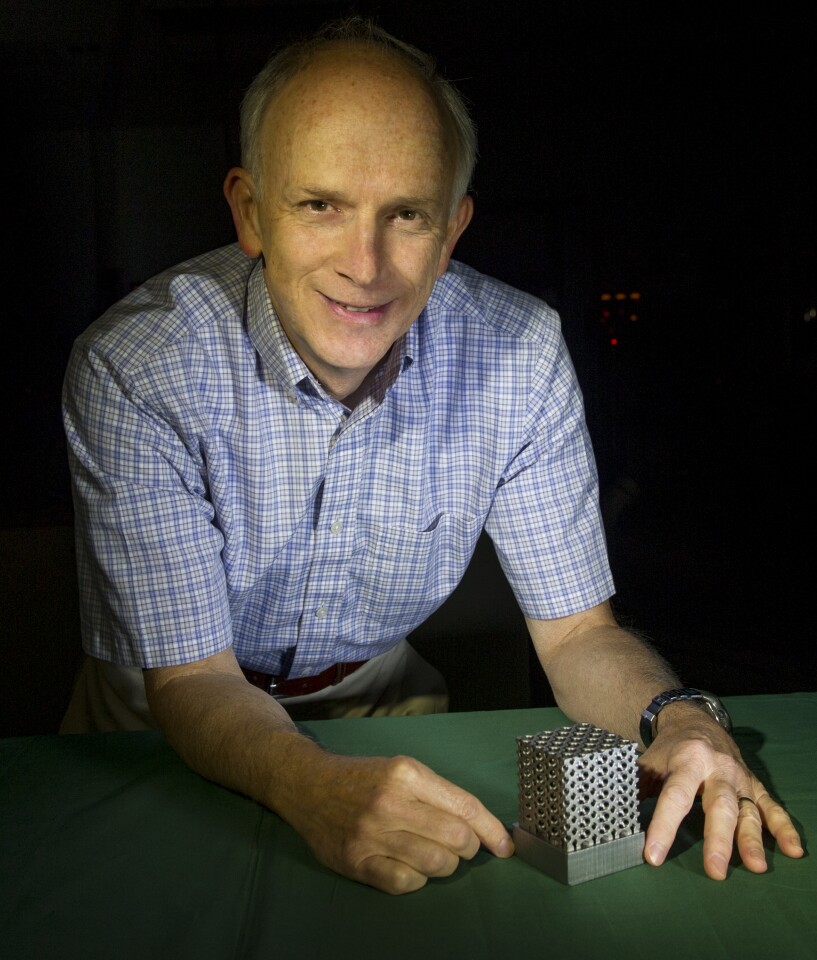
Budinoff’s current design is a fully functional, 50-mm (2-in) camera, which is small enough to mount in a CubeSat. The outer tube, baffles and optical mounts are all printed as single structures from aluminum and titanium powder, and the only parts not printed are the glass mirrors and lenses. In all, the telescope has only four 3D-printed parts, where a similar instrument made conventionally would require 40 parts. However, this first prototype is strictly experimental and not meant for spaceflight.
"This is a pathfinder," says Budinoff. "When we build telescopes for science instruments, it usually involves hundreds of pieces. These components are complex and very expensive to build. But with 3D printing, we can reduce the overall number of parts and make them with nearly arbitrary geometries. We’re not limited by traditional mill- and lathe-fabrication operations."
According to Budinoff, a 3D-printed mirror would also simplify space telescope design – especially for infrared devices operating at cryogenic temperatures. At the moment, such telescopes use a variety of materials with different thermal properties that interact with one another in complicated and aggravating ways that engineers have to find techniques to neutralize. By decreasing the number of components and making them of similar materials, the problems become simpler as well.
The first prototype is scheduled to be completed next month and will be subjected to vibration and thermal-vacuum testing next year. The next phase of the project will be to build a 350-mm (14-in) dual-channel telescope. This will also include experiments with an iron-nickel alloy called Invar which has extreme dimensional stability over a range of temperatures, that could make for much more stable instruments.
Budinoff says that he also wants to be able to print the mirrors as well using powdered aluminum. Currently, this isn't possible because printed mirrors are too porous to take a polish, but by using a process called hot isostatic pressing, it may be possible to squeeze a thin layer of aluminum in a pressure chamber using an inert gas at 15,000 psi to a suitable density.
Source: NASA