Though there have been tremendous advances in space technology in recent years, when it comes to getting into space, we're still like cavemen trying to get beyond the breakers on a floating log – at least, that's the view of New Zealand-based company Rocket Lab. In the hopes of increasing the number of satellite launches to over 100 a year and placing constellations of small satellites into orbit numbering in the thousands, the company has developed a "battery-powered" rocket engine to lift its Electron launch vehicle at almost a tenth of the cost of conventional boosters.
Liquid rocket engines are hungry beasts that require huge quantities of propellants for every second of flight. To manage this, engines use turbopumps to feed propellants into the combustion chamber. In a conventional design, a centrifugal or axial-flow turbopump is driven by a gas turbine. This has done the job very well since the first rocket turbopumps were developed in the 1940s, but they're complex, heavy affairs that need their own fuel systems to operate.
Rocket Lab's idea for making a lighter, simpler liquid rocket is its Rutherford engine. Named after New Zealand-born physicist Ernest Rutherford, it's an electric turbopump engine that burns a mixture of liquid oxygen and RP-1 rocket fuel, which is a highly refined type of kerosene. Unlike conventional engines, in the Rutherford, the gas-powered turbine to run the pump is replaced with a brushless DC motor and lithium polymer batteries, and provides enough fuel for the Rutherford to generate 4,600 lbf (20,462 N) of thrust and a specific impulse of 327 seconds.
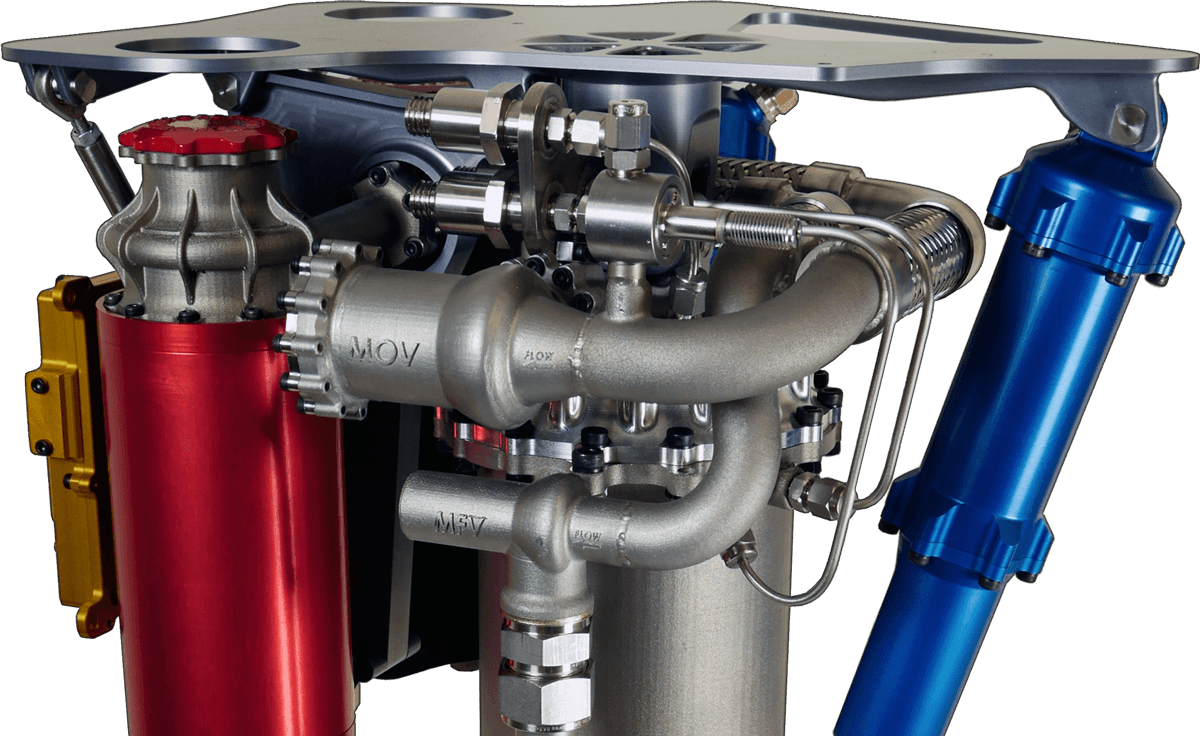
The company says that the Rutherford is also notable as the first oxygen/hydrocarbon engine to use 3D printing for all its primary components, including the regeneratively cooled thrust chamber, injector, pumps, and main propellant valves.
The Electron itself is a two-stage rocket measuring 1 m (3.2 ft) in diameter and 20 m (65.6 ft) high, and is designed to lift a 100 kg (220 lb) payload into a 500 km (310 mi) Sun-synchronous orbit. This is due, in part, to its extremely light carbon-composite construction, which, according to Rocket Lab, gives it a dry weight that's lighter than a Mini Cooper. These composites not only allow for bespoke construction with the tanks and other components designed with strength only in the needed directions, but also for tanks compatible with liquid oxygen combined with a proprietary thermal protection system for the cryogenics.
According to Rocket Lab, there are not only nine Rutherford engines in the first stage producing 34,500 to 41,500 lbf (153,464 – 184,602 N) of thrust, but the second stage uses a variant of the Rutherford engine designed to work more efficiently in the vacuum of space. The vacuum variant differs only in nozzle shape, with the same basic engine design for both stages providing for faster production.
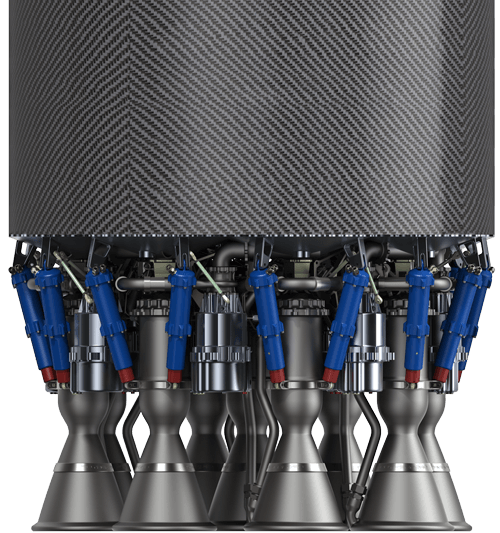
Another innovation for the Electron is its two-axis thrust vector control system for launching in strong winds, and its advanced avionics system weighing 19 lb (8.6 kg). The launcher also uses a plug-and-play system to prevent cascading delays and allows customers to provide alternative payloads at short notice.
Rocket Lab says that when the system is up and running, the Electron booster will be able to lift a payload into orbit using less fuel than a 737 flying from New York to Los Angeles, and will cost US$4.9 million per launch. This is a 91 percent saving on current launch costs, with Rocket Lab using an all-in-one launching service by providing not only the rocket, but also the commercial launch facility in New Zealand.
The first flight of the Electron launch system is slated for later this year with commercial operations targeted to begin in 2016.
The system is described in the video below.
Source: Rocket Lab