Back in April, we first heard about a 3D-printed UAV airframe that could be fabricated within 24 hours. Created by a Boeing-assisted team at the University of Sheffield's Advanced Manufacturing Research Center, it was a gliding prototype that would require the addition of a motor and an external propeller for powered flight. Its recently-announced successor, however, features integrated electric ducted fan motors.
As with its predecessor, the modular components of the new blended-wing UAV were made largely via Fused Deposition Modeling (FDM). This is the type of 3D printing in which successive layers of molten plastic are extruded one on top of another, to build up complete objects.
Although the aircraft consists of separate modules that are bolted together, the central body – which houses the fan motors and incorporates "complex internal features" – was printed as a single ABS plastic part. The motors and electronics themselves were added afterwards.
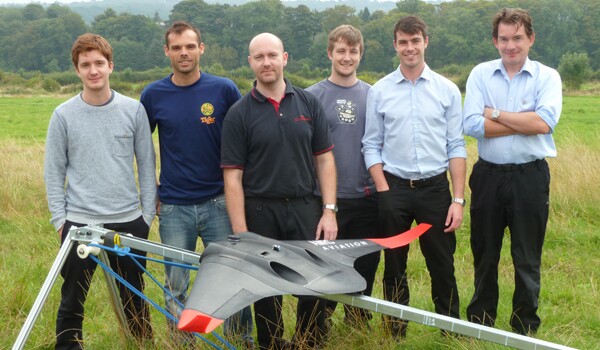
While some other components were made from carbon fiber this time around (it presumably now takes a little longer than 24 hours to build), those parts were still made using 3D-printed molds. As an added economical bonus, those molds were double-sided, allowing one piece of plastic to be used to create two parts. One of those carbon parts is a moveable "duck tail," which facilitates improved pitch control by channeling the air as it comes out of the ducts.
The finished UAV weighs 3.5 kg (7.7 lb), puts out 2.5 kg (5.5 lb) of combined thrust, cruises via remote control at nearly 72 km/h (45 mph), and is launched using a custom-made catapult.
Plans call for the next version to have a twice-as-wide 3-meter (9.8-ft) wingspan and miniature gas turbine engines. It may also incorporate unique flight control surfaces, and carbon composite batteries that are part of its structure.
Sources: University of Sheffield, AMRC paper